
Mars Pathfinder Airbags
The Mars Pathfinder airbag system was designed to protect the lander
regardless of its orientation upon impact with the surface of the planet.
The system also was designed to handle lateral movement as well as vertical
descent.
The result is a robust system capable of landing in rugged but scientifically
interesting locations at Mars. Development of the airbags required significant
design and test work, but the qualification program for the system was completed
in April of 1996, 8 months prior to launch.
See how the airbag system fits in the entire Entry,
Descent and Landing process.
Layout drawing of a single airbag
Each airbag is configured as six, 0.9 m radius spheres spaced on 1.0
m centers. Internal and external straps or tendons hold the airbag to the
lander at six locations.
Overall configuration of the lander with four airbags surrounding
it
The airbags are made out of a high strength fiber called Vectran. They
are constructed with an airtight bladder layer surrounded by four layers
of a slightly lighter Vectran fabric. The multiple layers of a lighter weave
was found to work better than a single layer of a heavier weave of Vectran.
Sandia National Laboratory helped JPL
do the early design and analysis of the airbag concept. ILC
Dover, Inc. built and tested the airbags.
An early 3-lobed airbag configuration
Shown here during retraction testing, an engineering model 8-wheel rover is in the foreground.
Full-scale airbag and lander suspended in a test chamber
The Space Power Facility (SPF) at NASA's Lewis Plum Brook Station (part
of NASA's Lewis
Research Center) is the world's largest vacuum chamber. The airbags
and lander were dropped in this facility in order to simulate martian atmospheric
pressures (1/100 of Earth's). The photo shows the airbags suspended 20 feet
above an impact platform just prior to door closing.
An engineer in front of the suspended airbags prior to chamber
door closure
The airbags were dropped onto a flat platform from 30 and 70 feet to
test their performance. Catch nets surround the platform to contain the
airbags when they bounce. The test was a giant slam dunk! It worked great!
A more difficult drop test configuration
After testing on a flat, smooth platform, engineers made things tougher
by raising the platform to a 60 degree angle and placing rocks on its surface.
In order to get the airbags and and lander (about 800 pounds total) up to
nearly 60 mph for the tests, engineers had to invent and build a giant bungie
cord accelerator. The bungie cords pulled on the lander with about 2000
pounds of force, and only releasing when the assembly hit the platform.
The catch nets
Giant, energy-absorbing catch nets were necessary to catch the lander
and airbags after they hit the platform at 60 mph. The top of the platform
stands nearly 50 feet high.
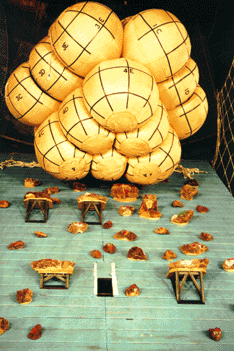 |
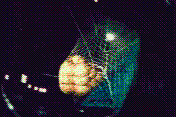
899K |
Drop test impact site |
MPEG Video of the drop test (courtesy of NASA Lewis Research
Center) |
The black markings on the airbags were used to help see what was happening
in the high speed film taken of each test. The slot in the center of the
platform is where the bungie accelerator tow line passed through. The large
rocks (supported with steel backing) stand 1 m high. They were all hand
picked by a JPL planetary geologist to represent the closest match to actual
Mars rocks. (And they were very sharp and nasty!)
A puncture
This is a close-up view of a medium-sized hole (about 12 inches long)
torn in the airbags during drop testing. Early testing resulted in multiple,
large (18-24 inch long) tears in the fabric. As you can see, the airbags
are constructed of a relatively thin bladder surrounded by a heavy-duty
outer abrasion layer.
The repair
ILC Dover technician Eleanor
Foraker repaired the airbags after each test. Four complete airbag systems
were built for testing. Stiching dozens of layers of this nearly bulletproof
material was never easy, but always necessary. Eleanor was also the woman
who sewed Neil Armstrong's and Buzz Aldrin's moonsuits for the Apollo 11
mission!
Inspection after repairs were complete
Sixteen drop tests were performed under different conditions and with
many different types of abrasion layer constructions. Here the airbags are
shown during the rigorous inspection done after any repair work. After each
test, engineers and technicians meticulously inspected every stich and seam
in the airbags and documented any damage.
Success!
Engineers in the control room cheer after a successful test!
Installing the airbags
ILC Dover engineers installed
the airbags into very tight bundles around the test lander in preparation
for a high speed inflation test. Extremely precise packaging of the airbags
was necessary in order to balance properly the whole spacecraft and to make
sure the airbags unfolded correctly when they were deployed.
The gas generators
With casings made out of titanium, three gas generators built by the
Thiokol Corporation are used to inflate
the airbags. The airbags go from being stowed to fully inflated in less
than 1 second. This "explosive" inflation is done by using solid
rocket propellant in the gas generator. The exhaust byproducts of the rocket
fuel inflate the airbag. Thermal heaters can be seen on two of the three
gas generators above.
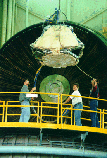 |
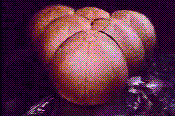
868K |
A fully packaged lander |
MPEG video of the inflation test (courtesy of NASA Lewis Research
Center) |
Here, a completely packaged lander with airbags and gas generators installed,
is lowered into a test chamber to perform a high speed inflation test. Before
inflating the airbags, the chamber was cooled to -80degC using liquid nitrogen.
Nearly all the air was also removed from the chamber. Once the airbags cooled,
the gas generators were ignited and the airbags inflated.
Retraction testing
See the movie!
Retraction tests were performed to make sure the airbag fabric could
be pulled out of the way before the lander was opened. In this picture you
see the lander with a rover on it, partially opened. In the foreground in
the airbag fabric partially retracted. Tiny, high-strength cables and a
miniature winch inside the airbag are used to perform the retraction.
Back to the Mission Objectives
Page
Back to the Mars Pathfinder Home Page